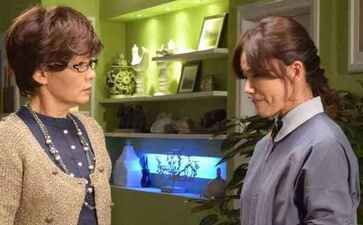
朝陽縣針城羊毛有限公司位于合川區(qū),朝陽縣針城羊毛有限公司www.tzbaigela.com經營范圍含:玩具娃娃、民間工藝品、蠶繭、網絡工程、音樂影片、玻璃包裝、玻璃制品、卡車、充電器、燃料(依法須經批準的項目,經相關部門批準后方可開展經營活動)。。
朝陽縣針城羊毛有限公司將堅定不移地貫徹落實黨中央和國務院關于國有企業(yè)深化改革的重要決策部署,緊密遵循國資委關于壯大和強化國有企業(yè)的具體要求。在此基礎上,我們將持續(xù)推進企業(yè)的深化改革進程,致力于進一步優(yōu)化產業(yè)結構,實現(xiàn)資源的科學配置,從而有效提升企業(yè)的核心競爭力。我們還將致力于全面提升企業(yè)的整體素質,使其能夠更好地適應并應對國際與國內市場的挑戰(zhàn)與機遇。我們將瞄準更為遠大的目標,不懈奮斗,努力將企業(yè)發(fā)展推向新的高度。
朝陽縣針城羊毛有限公司在發(fā)展中注重與業(yè)界人士合作交流,強強聯(lián)手,共同發(fā)展壯大。在客戶層面中力求廣泛 建立穩(wěn)定的客戶基礎,業(yè)務范圍涵蓋了建筑業(yè)、設計業(yè)、工業(yè)、制造業(yè)、文化業(yè)、外商獨資 企業(yè)等領域,針對較為復雜、繁瑣的行業(yè)資質注冊申請咨詢有著豐富的實操經驗,分別滿足 不同行業(yè),為各企業(yè)盡其所能,為之提供合理、多方面的專業(yè)服務。
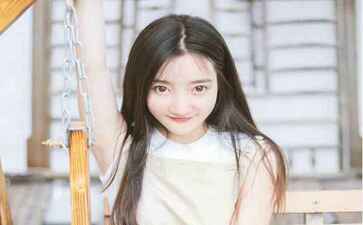
朝陽縣針城羊毛有限公司秉承“質量為本,服務社會”的原則,立足于高新技術,科學管理,擁有現(xiàn)代化的生產、檢測及試驗設備,已建立起完善的產品結構體系,產品品種,結構體系完善,性能質量穩(wěn)定。
朝陽縣針城羊毛有限公司是一家具有完整生態(tài)鏈的企業(yè),它為客戶提供綜合的、專業(yè)現(xiàn)代化裝修解決方案。為消費者提供較優(yōu)質的產品、較貼切的服務、較具競爭力的營銷模式。
核心價值:尊重、誠信、推崇、感恩、合作
經營理念:客戶、誠信、專業(yè)、團隊、成功
服務理念:真誠、專業(yè)、精準、周全、可靠
企業(yè)愿景:成為較受信任的創(chuàng)新性企業(yè)服務開放平臺
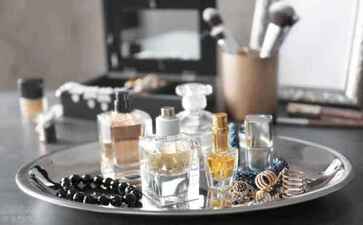